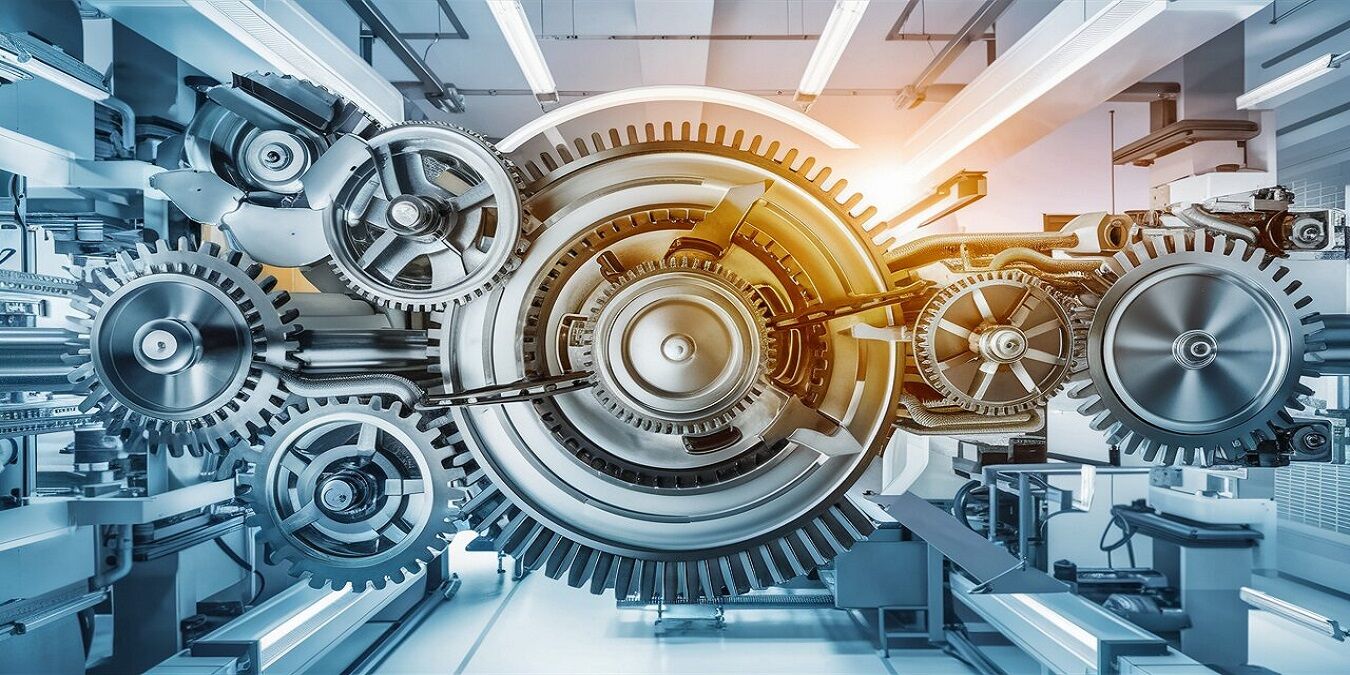
Optimizing Processes for Business Growth
In today’s highly competitive and fast-paced business environment, the mantra “Do More with Less” has become a crucial guiding principle for many organizations. The concept revolves around maximizing efficiency and productivity while minimizing resource consumption and waste.
This approach not only drives cost savings but also fosters innovation, improves customer satisfaction and enhances overall business growth.
This article delves into the strategies and methodologies that businesses can employ to optimize processes for growth, emphasizing the importance of lean principles, technological advancements and continuous improvement.
Embracing Lean Principles
Lean principles, originating from the manufacturing sector, particularly the Toyota Production System, focus on value creation with minimal waste. These principles are broadly applicable across various industries and can serve as a strong foundation for process optimization. The core concepts include.
- Identifying Value: Understand what constitutes value from the customer’s perspective. This involves direct engagement with customers to ascertain their needs and preferences. Clear insights into customer expectations allow businesses to tailor their processes to deliver maximum value.
- Value Stream Mapping: This involves mapping out all the steps in a process to identify and eliminate non-value-adding activities. By creating a visual representation of the workflow, organizations can pinpoint inefficiencies and areas that can be streamlined.
- Creating Flow: Ensure that the process flows smoothly without interruptions or bottlenecks. A well-coordinated workflow reduces delays and enhances the speed of delivery. Techniques such as cellular manufacturing, continuous flow and load leveling can be employed to maintain a steady flow.
- Establishing Pull Systems: Implement systems where production is based on actual demand rather than forecasts. This minimizes overproduction and inventory costs. Just-In-Time (JIT) production is a classic example of a pull system that aligns production schedules with customer orders.
- Striving for Perfection: Continuous improvement (Kaizen) is a central tenet of lean principles. By fostering a culture of constant refinement and encouraging employee involvement, organizations can achieve incremental yet significant improvements over time.
Leveraging Technological Advancements
Technology plays a pivotal role in process optimization. Organizations that leverage cutting-edge technologies can significantly enhance their operational efficiency, reduce costs and drive growth. Key technological advancements include.
- Automation and Robotics: Automating repetitive and mundane tasks frees up human resources for more strategic and creative endeavors. Robotics and process automation can enhance precision, reduce errors and increase production speed. For example, robotic process automation (RPA) can streamline data entry, invoice processing and other administrative tasks.
- Data Analytics and Business Intelligence: Data-driven decision-making is imperative in optimizing processes. Advanced analytics tools can provide insights into operational performance, customer behavior and market trends. By analyzing this data, organizations can identify areas for improvement and make informed decisions that drive efficiency and growth.
- Enterprise Resource Planning (ERP) Systems: ERP systems integrate various business processes into a unified system, providing real-time visibility and control over operations. This integration enhances coordination across departments, reduces redundancies and improves resource allocation.
- Internet of Things (IoT): IoT devices can collect real-time data from machinery, equipment and other assets. This data can be used to monitor performance, predict maintenance needs and optimize asset utilization. For instance, IoT sensors in manufacturing can help prevent downtime by predicting equipment failures before they occur.
- Cloud Computing: Cloud-based solutions offer scalability, flexibility and cost savings. By adopting cloud technologies, organizations can streamline their IT infrastructure, improve collaboration,and access advanced analytics tools without significant upfront investments.
Adopting Agile Methodologies
Agile methodologies, initially developed for software development, have gained traction across various industries for their flexibility and focus on customer satisfaction. Core agile principles that contribute to process optimization include.
- Iterative Development: Breaking down projects into smaller, manageable segments allows for continuous feedback and adjustments. This iterative approach ensures that processes remain aligned with evolving customer needs and market conditions.
- Cross-Functional Teams: Agile emphasizes collaboration among diverse teams to enhance innovation and problem-solving. By leveraging the collective expertise of individuals from different departments, organizations can develop more efficient and effective processes.
- Customer-Centric Approach: Agile methodologies prioritize delivering value to customers through iterative releases and feedback loops. By continuously engaging with customers and incorporating their feedback, organizations can refine processes to better meet customer expectations.
- Adaptability: Agile promotes a culture of adaptability and responsiveness to change. In an ever-evolving business landscape, the ability to pivot and adjust processes quickly is crucial for sustaining growth.
Fostering a Culture of Continuous Improvement
Creating a culture of continuous improvement is essential for sustainable process optimization. This involves.
- Empowering Employees: Employees are often the best source of insight for identifying inefficiencies and suggesting improvements. Organizations should empower employees by soliciting their input, providing training and creating an environment where they feel comfortable proposing and implementing changes.
- Setting Clear Goals and Metrics: Establish clear, measurable goals for process improvements. Key performance indicators (KPIs) and other metrics help track progress and identify areas where further refinement is needed. Regularly reviewing these metrics fosters accountability and ensures that optimization efforts are aligned with business objectives.
- Encouraging Innovation: Encourage a mindset where experimentation and innovation are part of the company culture. Organizations can adopt practices such as hackathons, innovation labs or dedicated time for employees to work on personal projects that could lead to process improvements.
- Reward and Recognition Programs: Recognize and reward employees who contribute to process optimization. Acknowledging their efforts fosters a sense of ownership and motivates others to engage in continuous improvement initiatives.
Streamlining Supply Chain Management
A robust and efficient supply chain is vital for optimizing business processes. Key strategies include.
- Supplier Collaboration: Foster strong relationships with suppliers to improve communication, coordination and reliability. Sharing demand forecasts and collaborating on inventory management can reduce lead times and optimize stock levels.
- Demand Planning and Inventory Management: Utilize advanced forecasting techniques and inventory management systems to accurately predict demand and maintain optimal inventory levels. This approach reduces excess stock, minimizes storage costs and ensures timely delivery to customers.
- Logistics Optimization: Streamline logistics operations by leveraging technologies such as route optimization software, real-time tracking and automated warehousing systems. Efficient logistics minimize transportation costs and improve delivery speed.
- Sustainability: Integrating sustainable practices into the supply chain can lead to cost savings and process efficiencies. For instance, reducing packaging waste, optimizing transportation routes and adopting eco-friendly materials can enhance both environmental and operational performance.
Enhancing Customer Experiences
Customer satisfaction is a key driver of business growth. Optimizing processes with a focus on enhancing customer experiences can lead to higher retention rates and increased revenue. Strategies include.
- Personalization: Utilize customer data to tailor products, services and communications to individual preferences. Personalized experiences drive customer loyalty and increase satisfaction.
- Customer Feedback Loops: Establish channels for collecting and acting on customer feedback. Regularly gathering insights from customers and using this information to refine processes ensures that they remain aligned with customer needs.
- Responsive Customer Service: Implement efficient customer service processes with quick response times, multichannel support options and proactive issue resolution. Happy customers are more likely to become repeat buyers and brand advocates.
- User-Friendly Interfaces: For businesses with digital touchpoints, such as websites or mobile apps, ensuring a seamless and intuitive user experience is critical. Regularly updating and optimizing these interfaces based on user feedback can significantly enhance customer satisfaction.
Investing in Employee Development
Optimizing processes for business growth is not solely about technology and systems – people are at the heart of any organization. Investing in employee development is crucial for sustained optimization.
- Training Programs: Offer comprehensive training programs to equip employees with the skills and knowledge needed to operate new technologies and adopt improved processes effectively.
- Leadership Development: Develop leadership at all levels to nurture a culture that values continuous improvement. Leaders play a crucial role in championing process optimization initiatives and motivating their teams.
- Succession Planning: Plan for the future by identifying and developing potential leaders within the organization. A strong pipeline of capable leaders ensures that process optimization efforts continue smoothly even as personnel changes occur.
Case Studies and Success Stories
To illustrate the impact of optimizing processes for business growth, consider the following examples.
- Toyota: The pioneer of lean manufacturing, Toyota has consistently optimized its production processes to minimize waste and maximize value. Their just-in-time approach and continuous improvement culture have enabled them to maintain high-quality standards and achieve significant cost savings.
- Amazon: Amazon’s focus on optimizing logistics and inventory management has revolutionized the e-commerce sector. Their use of data analytics, automation and strategic supplier relationships has allowed them to offer rapid delivery times and maintain a vast inventory with minimal waste.
- Zara: The fashion retailer Zara uses a highly responsive supply chain to ensure that new designs reach stores quickly. By keeping inventory levels low and relying on small, frequent shipments, Zara can adapt swiftly to changing fashion trends, reducing excess inventory and markdowns.
Conclusion
The journey to doing more with less is an ongoing process that requires a multifaceted approach.
By embracing lean principles, leveraging technological advancements, adopting agile methodologies, fostering a culture of continuous improvement, streamlining supply chain management, enhancing customer experiences and investing in employee development, organizations can optimize their processes for sustainable business growth.
In an era where efficiency and agility can make or break a business, optimizing processes is not just a strategic advantage but a necessity. Companies that commit to continuous improvement and adopt a holistic approach to process optimization will be best positioned to thrive in a competitive landscape and drive sustained growth.