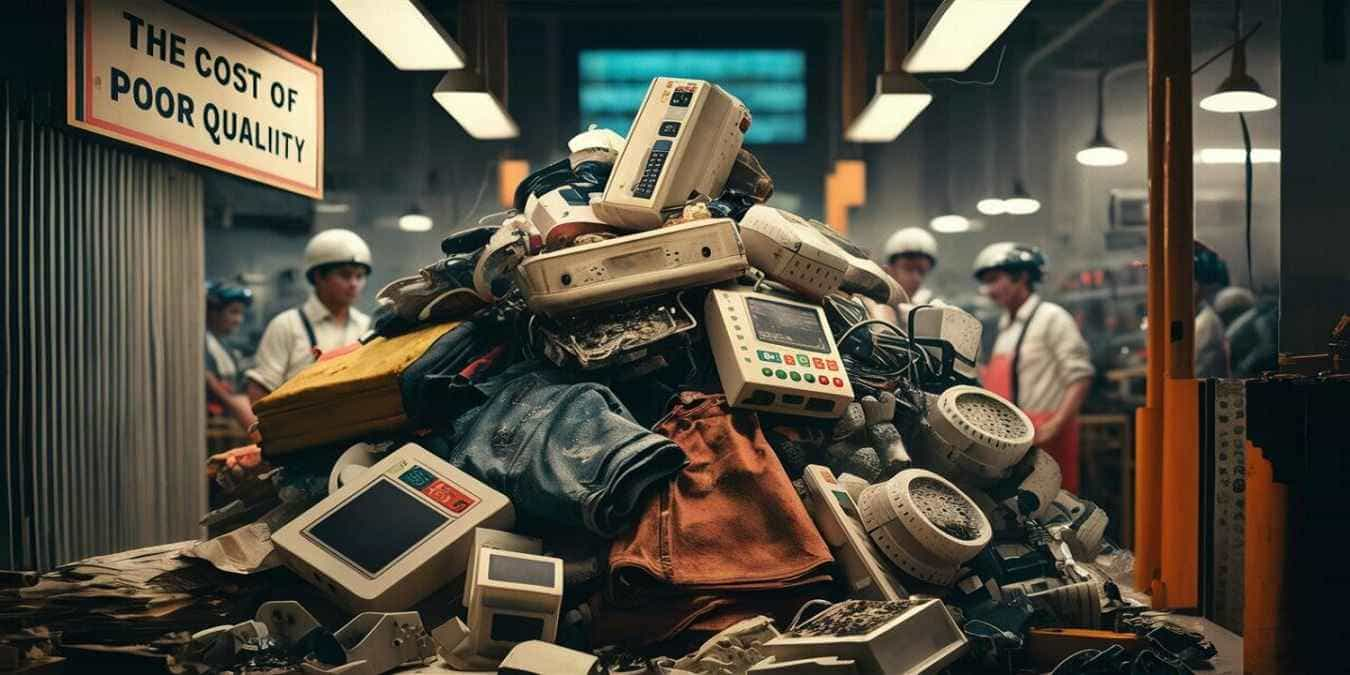
What is the Cost of Poor Quality?
The Cost of Poor Quality (COPQ) refers to expenses incurred when products, services or processes fail to meet quality standards. It’s the money a business loses when things go wrong. These costs can be classified into four categories.
- Internal Failure Costs: Costs incurred to correct defects before the product reaches the customer. This includes rework, scrap and downtime.
- External Failure Costs: Costs associated with defects found after the product has been delivered to the customer. This includes warranty claims, returns and repairs.
- Appraisal Costs: Costs incurred to determine the degree of conformance to quality requirements. This includes inspection, testing and audit costs.
- Prevention Costs: Costs incurred to prevent defects from occurring. This includes quality planning, training and preventive maintenance.
Understanding these categories helps businesses identify where they might be incurring unnecessary expenses and how they can improve their processes to reduce these costs.
The Financial Impact of Poor Quality
The financial ramifications of poor quality are significant and multifaceted. Here are some of the direct and indirect costs associated with poor quality.
Direct Costs
- Rework and Scrap: Defective products need to be reworked or scrapped, leading to increased material and labor costs. These activities consume resources that could otherwise be used for producing quality products.
- Warranty Claims and Returns: Products that fail to meet quality standards often result in warranty claims and returns. These not only incur direct costs but also affect the company’s bottom line due to lost sales and increased customer service expenses.
- Inspection and Testing: Increased inspection and testing to identify defects add to the overall production costs. While necessary to ensure quality, excessive reliance on these activities indicates underlying quality issues.
Indirect Costs
- Lost Sales and Market Share: Poor quality products lead to dissatisfied customers, negative reviews and loss of repeat business. This can significantly impact sales and reduce market share.
- Damage to Brand Reputation: Consistently delivering poor quality products damages a company’s reputation. Recovering from a tarnished brand image can be challenging and expensive.
- Legal Costs: Defective products can lead to lawsuits, regulatory fines and compliance issues. Legal battles not only drain financial resources but also distract management from core business activities.
- Employee Morale and Productivity: Working in an environment plagued by quality issues can demoralize employees. Low morale leads to decreased productivity, higher absenteeism and increased turnover rates.
The Hidden Costs of Poor Quality
Beyond the obvious financial impacts, poor quality also incurs several hidden costs that can be equally damaging.
- Opportunity Costs: Time and resources spent on addressing quality issues could be better utilized for innovation, expansion or other strategic initiatives.
- Customer Loyalty: Acquiring new customers is more expensive than retaining existing ones. Poor quality erodes customer loyalty, making it difficult to maintain a stable customer base.
- Supply Chain Disruptions: Quality issues can disrupt the supply chain, leading to delays, increased lead times and higher inventory costs. Suppliers and partners may lose confidence in the business, affecting collaboration and future opportunities.
- Impact on Competitive Advantage: Consistent quality problems can erode a company’s competitive edge, allowing competitors to capitalize on the opportunity to capture market share.
Measuring the Cost of Poor Quality
To effectively manage and reduce COPQ, businesses must first measure it accurately. Here are some steps to measure COPQ.
- Identify Quality-Related Costs: Categorize costs into internal failure, external failure, appraisal and prevention costs. This helps in understanding where most expenses are being incurred.
- Collect Data: Gather data on defect rates, rework, scrap, warranty claims, returns and other quality-related metrics. Use this data to quantify the costs associated with each category.
- Analyze Trends: Examine the data to identify trends and patterns. This helps in pinpointing recurring quality issues and their root causes.
- Benchmark Against Industry Standards: Compare your COPQ metrics with industry benchmarks to understand how your quality performance stacks up against competitors.
- Calculate Total COPQ: Sum up the costs from all categories to determine the total COPQ. This provides a clear picture of the financial impact of poor quality on the business.
Strategies to Reduce the Cost of Poor Quality
Reducing COPQ requires a proactive approach to quality management. Here are some strategies to help businesses minimize these costs.
- Implement a Quality Management System (QMS): A robust QMS helps in standardizing processes, improving consistency and reducing defects. It provides a framework for continuous improvement and ensures compliance with quality standards.
- Invest in Training and Development: Equip employees with the skills and knowledge necessary to maintain high-quality standards. Regular training sessions on quality control, problem-solving and process improvement can significantly reduce quality issues.
- Adopt Lean and Six Sigma Methodologies: Lean and Six Sigma are powerful methodologies for improving quality and reducing waste. These approaches focus on identifying and eliminating non-value-added activities, streamlining processes and enhancing overall efficiency.
- Enhance Supplier Quality Management: Collaborate closely with suppliers to ensure they meet your quality standards. Implement supplier audits, performance reviews and quality agreements to maintain consistency and reduce defects in the supply chain.
- Use Data Analytics and Automation: Leverage data analytics to gain insights into quality performance and identify areas for improvement. Automation tools can also help in reducing human errors and increasing process efficiency.
- Focus on Prevention: Shift the focus from detection to prevention. Invest in preventive measures such as process design, preventive maintenance and early-stage testing to catch and address potential quality issues before they escalate.
- Engage Customers in Feedback: Actively seek and analyze customer feedback to understand their expectations and areas where quality can be improved. Use this feedback to drive continuous improvement initiatives.
The Role of Leadership in Quality Management
Leadership plays a crucial role in fostering a culture of quality. Leaders must –
- Set Clear Quality Objectives: Define and communicate clear quality goals and expectations to all employees. Ensure that these objectives are aligned with the overall business strategy.
- Promote a Quality-First Mindset: Encourage a culture where quality is prioritized over speed and cost-cutting. Recognize and reward employees who demonstrate a commitment to quality.
- Allocate Resources Wisely: Ensure that adequate resources, including time, budget and personnel, are allocated to quality management initiatives. Invest in technology, training and tools that support quality improvement.
- Lead by Example: Demonstrate a commitment to quality through actions and decisions. Leadership behavior sets the tone for the entire organization.
Conclusion
The Cost of Poor Quality is a critical metric that businesses cannot afford to overlook. By understanding the direct, indirect and hidden costs associated with poor quality, companies can take proactive steps to improve their processes, reduce defects and enhance overall performance.
Implementing a comprehensive quality management strategy, supported by strong leadership and a quality-first mindset, can significantly reduce COPQ and drive long-term success. In today’s competitive business world, focusing on quality is not just about avoiding losses; it’s about building a sustainable, reputable and customer-centric business.
Tags: Cost of Poor Quality (COPQ) Quality Management Financial Impact Internal Failure Costs External Failure Costs Appraisal Costs Prevention Costs Process Improvement Lean Six Sigma Supplier Quality Management Customer Satisfaction Leadership in Quality
Information nicely considered.!